All you need to know about how to do a laser cutting and laser engraving using 60 watt Co2 laser with galvoscanner installed on CNC 6050 frame
The installation was used to complete the task. Which is based on the C NC 6050 machine with a CO 2 laser tube installed on it with a power of 60 W and a wavelength of 10600 nm. To cool the tube, a water cooling system is used to keep the tube temperature within 15° C . There is an additional mount on the frame of the machine, on which an RC 1001 galvanometer is installed , equipped with a lens with a focal length of 160 mm and a working area of 110×110 mm. The maximum speed of the laser beam on the working surface is 8000 mm/s. Two mirrors are used to guide the laser beam into the inlet of the galvanometer.
The installation is controlled using the EzCad program .
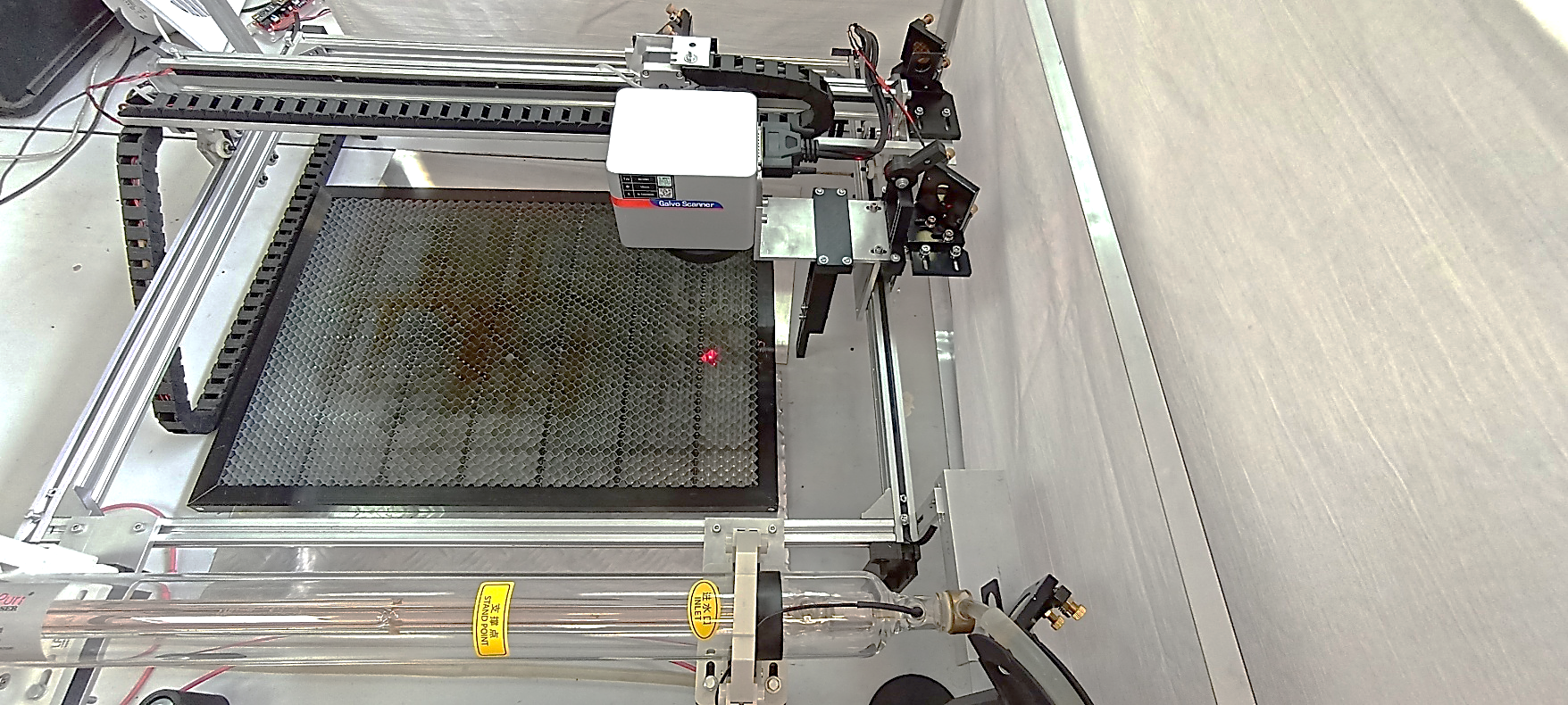
Cutting wood and acrylic materials:
In the course of work, we managed to find out that when cutting wood materials (MDF, plywood, laminated boards), deposits appear inside the cut channel, which clog the cut channel and begin to burn at a certain moment.
If the plywood is not very dense (0.4 g / cm 3 ), no damage to the material is observed, but fire appears during the cutting process, which should not be.
On laser CNC machines, a nozzle is used to prevent the appearance of fire, in the case of a galvanometer, it cannot be used.
with a thickness of 2.5 mm and a density of 0.4 g/ cm ).
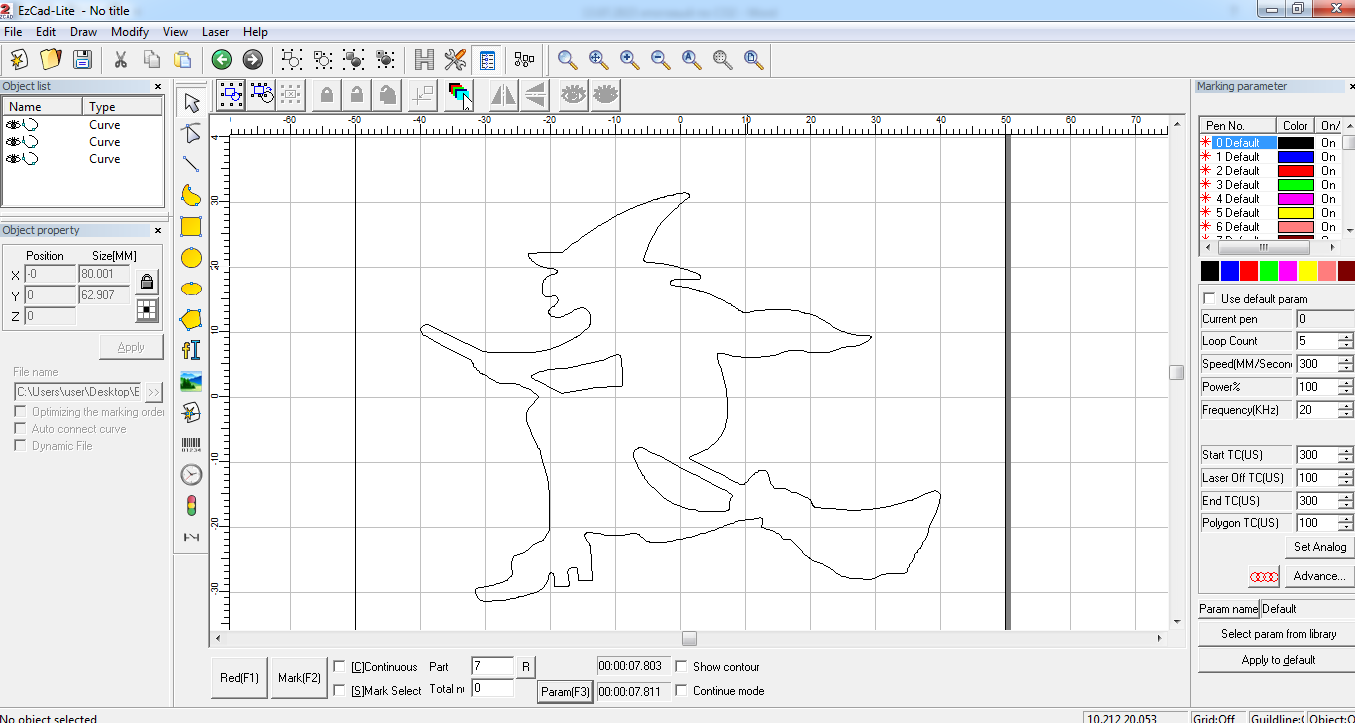
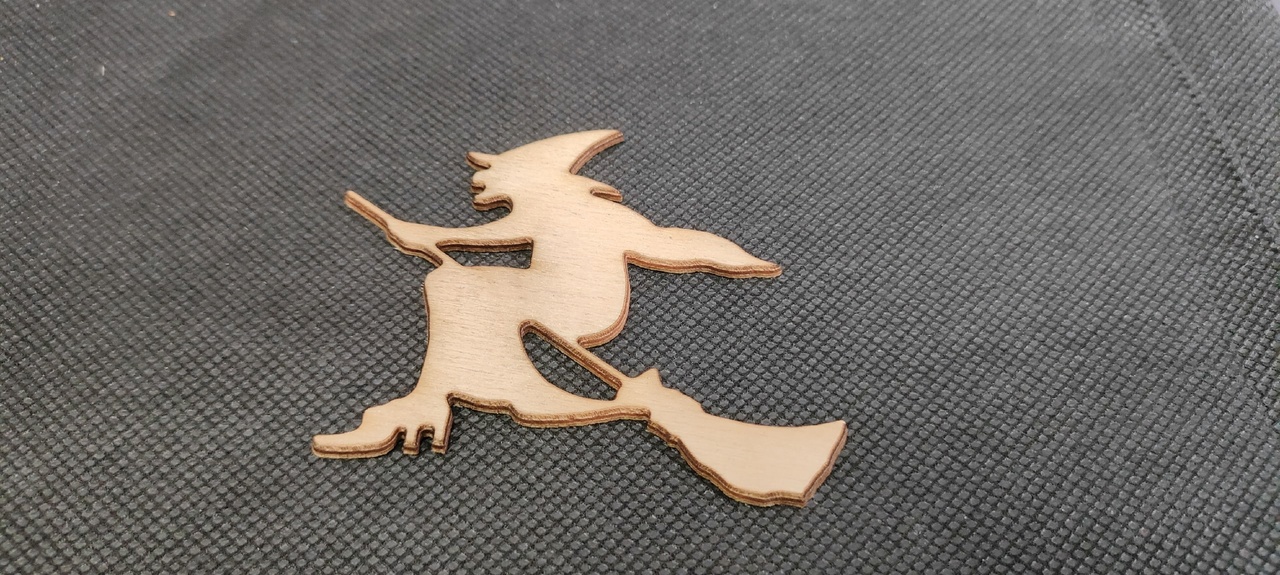
During the work, no damage was observed to the material, but during the cutting process, fire appears, which should not be.
To cut parts on acrylic with a large number of cut elements, we chose the original template (Fig. 3, a), then converted the template into a vector form and added it to the EzCad program .
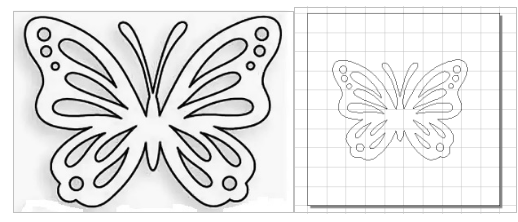
We also selected the optimal cutting parameters. For 3.2 mm thick acrylic, the pass speed was set to 100 mm/s, the number of passes was 7, and the laser power was set to 100%.
A positive result was obtained (Fig. 5), the material was not deformed.
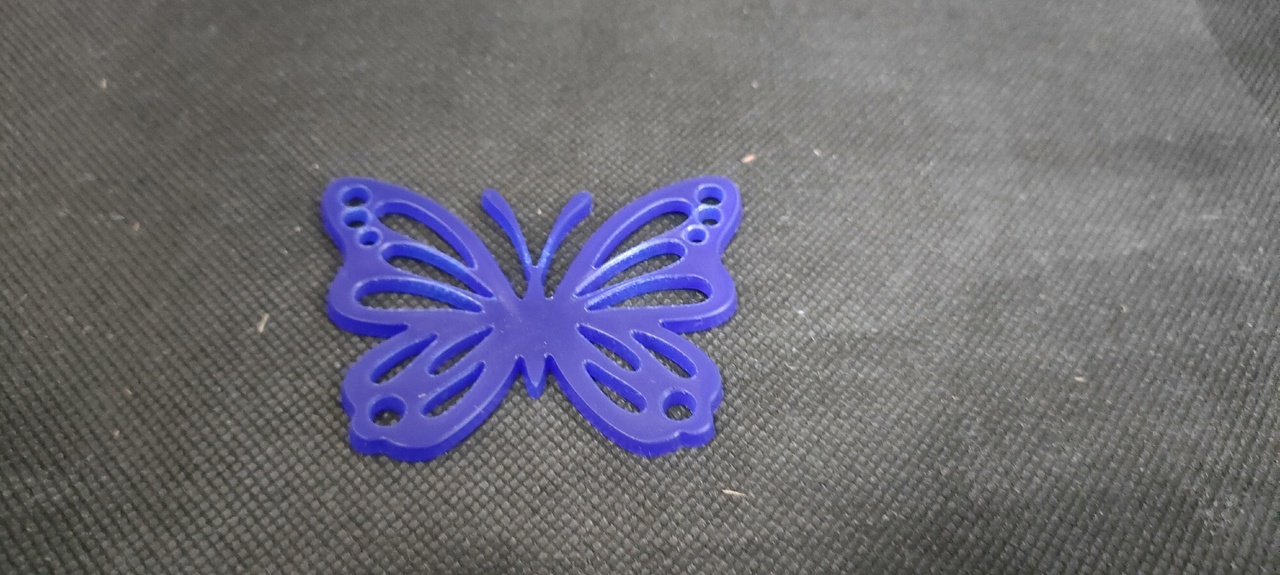
Prefabricated cutting on plywood and acrylic
There were attempts to cut a prefabricated structure (puzzle) on plywood with a thickness of 3.3 mm and a density of 0.68 g / cm 3 with a number of passes of 25 times, a pass speed of 1000 mm / s and a power of 100%.
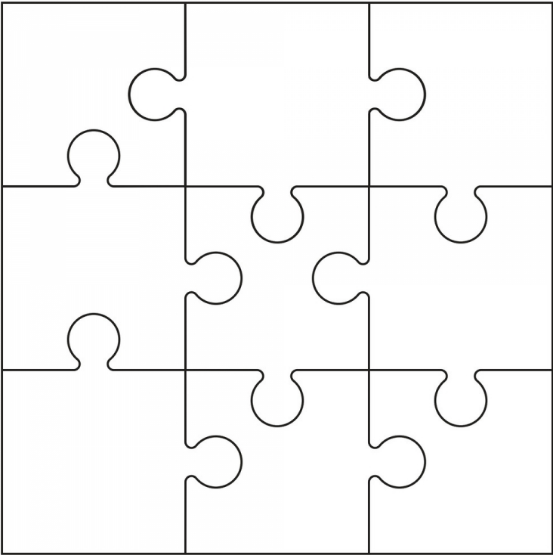
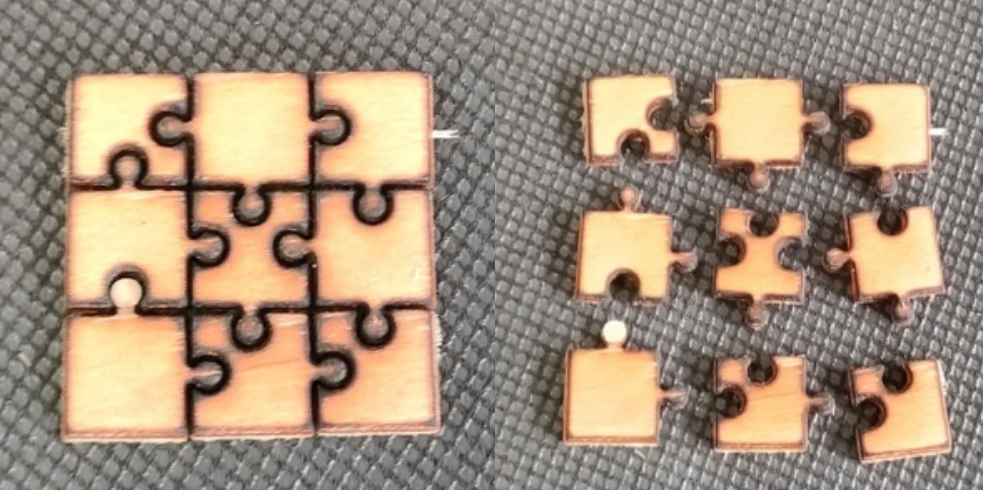
When trying to cut out the rocking horse constructor (Fig. 7). It turned out to cut out the details, but the grooves do not match.
In the case of the “plywood” material, no fire was observed during the cutting process, but the parts turned out to be too charred (Fig. 6). The grooves match, but the parts stick together weakly and almost do not stick together. This is due to the fact that the laser beam leaves the center of the galvanometer and its movement occurs due to the deflection of the galvanometer mirrors, therefore the laser beam interacts with the material not at a right angle, but at an acute angle, which during cutting operations gives a cut that is beveled towards the center of the worker fields.
For acrylic, the number of passes was 5 times, the pass speed was 100 mm/s, and the power was 100% (Fig. 8). When cutting a prefabricated structure (puzzle) on acrylic, the result was negative, because after cutting it was not possible to join the parts, the same effect was noticed when cutting plywood.
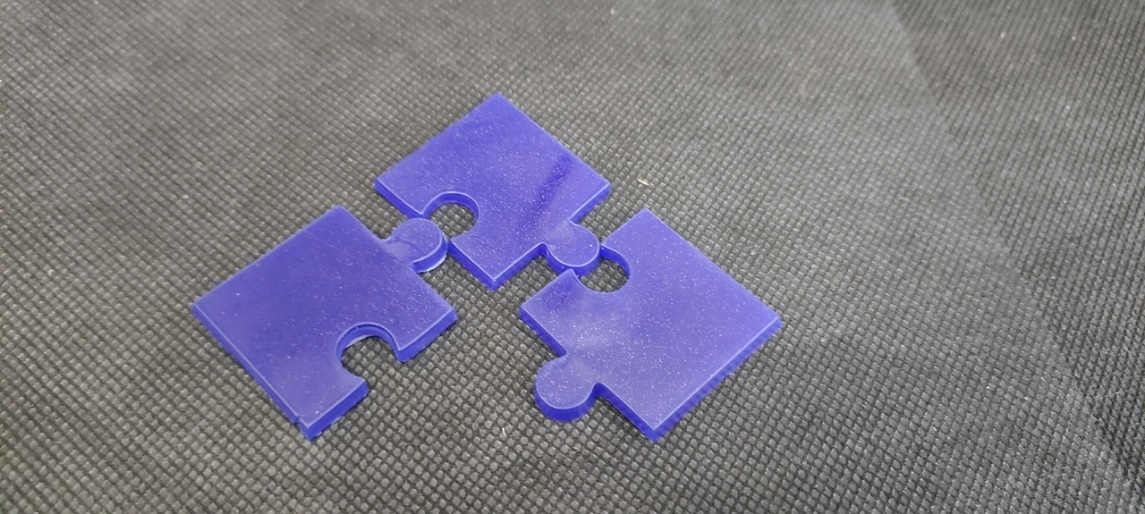
Thus, it makes no sense to cut complex prefabricated parts on this machine. Such cutting is problematic because of the very different cut angles of individual parts, and these angles are different in different places of the cut.
Fill engraving
We made engraving with pouring of such materials as MDF, plywood, transparent and colored acrylic, laminated board. To do this, the contour of the engraved drawing was entered into the EzCad program (Fig. 9).
Further, in the same program, the correspondence of each color layer of the picture and engraving parameters was established (Table 1). Parameters specified
Table 1 – Engraving parameters with filling for 1 sample
Layer color | Number of passes | Speed, mm/s | Power, % |
Black | 1 | 500 | 100 |
Blue | 1 | 1200 | 80 |
Red | 1 | 1400 | thirty |
Green | 1 | 900 | 100 |
Pink | 1 | 700 | 70 |
Yellow | 6 | 1000 | 100 |
The result of engraving with filling on MDF, plywood and laminated board is indicated in Figure 10 (a, b, c).
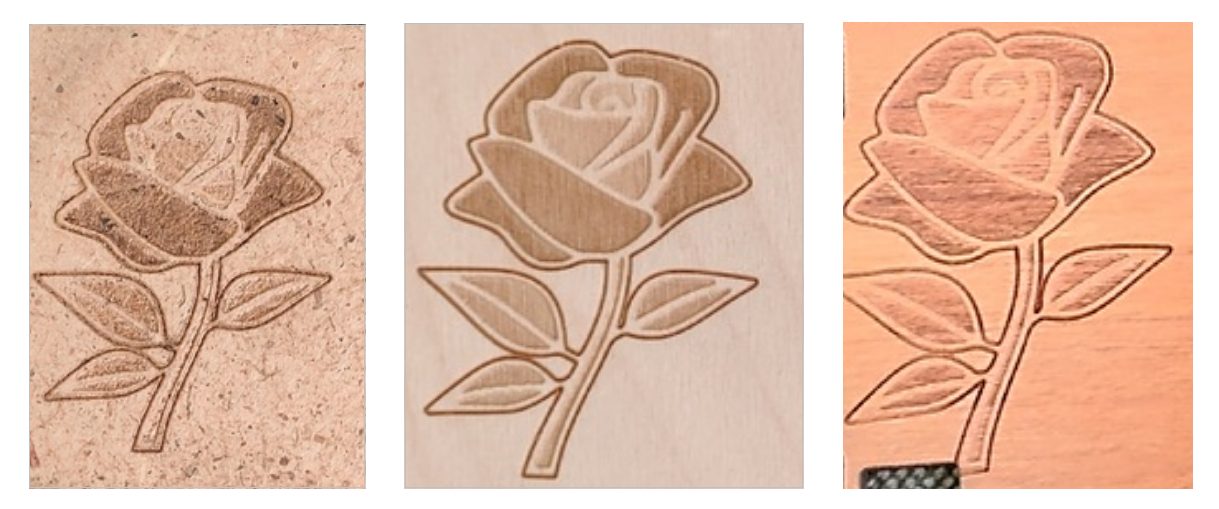
On plywood, the shades are clearly visible, but on MDF and laminated boards, due to the structure of the material, they are poorly visible.
For the acrylic material, the engraving parameters along the contour were used: the number of passes over the material 6 times, the speed was 1000 mm/s, and the power was 100%. Filling engraving parameters: number of passes over the material 1 time, speed 1400 mm/s and power 30% (Fig. 11).
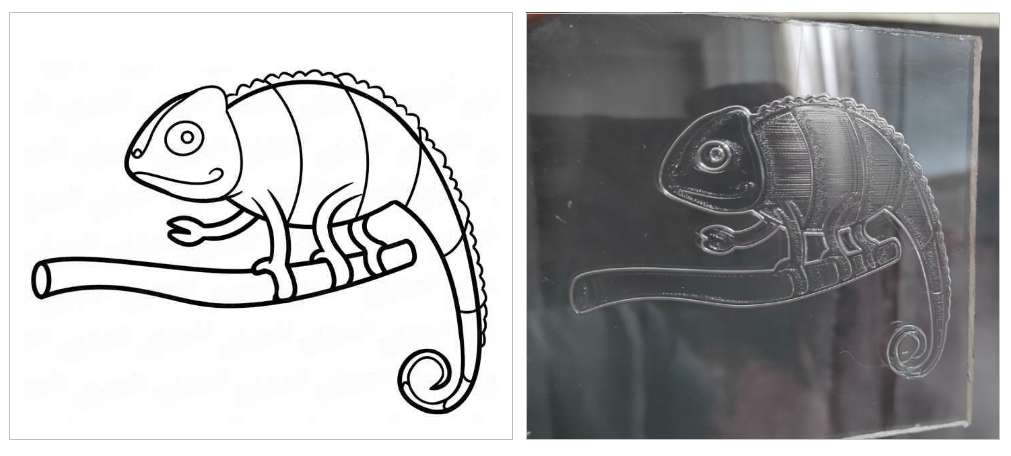
Contour engraving
For materials: MDF, plywood, acrylic, laminated board, the optimal parameters were used: the number of passes over the material 6 times, the passage speed was 1000 mm/s, the power was 100%. As a result of the engraving of MDF, plywood and acrylic, the appearance of fire was not observed. When engraving a laminated board, the appearance of fire for a fraction of a second was noticed, but this factor did not affect the engraving result and the quality of the material.
a) dragon source b) lizard source
c) the source of the horse
Figure 12 – Engraving source
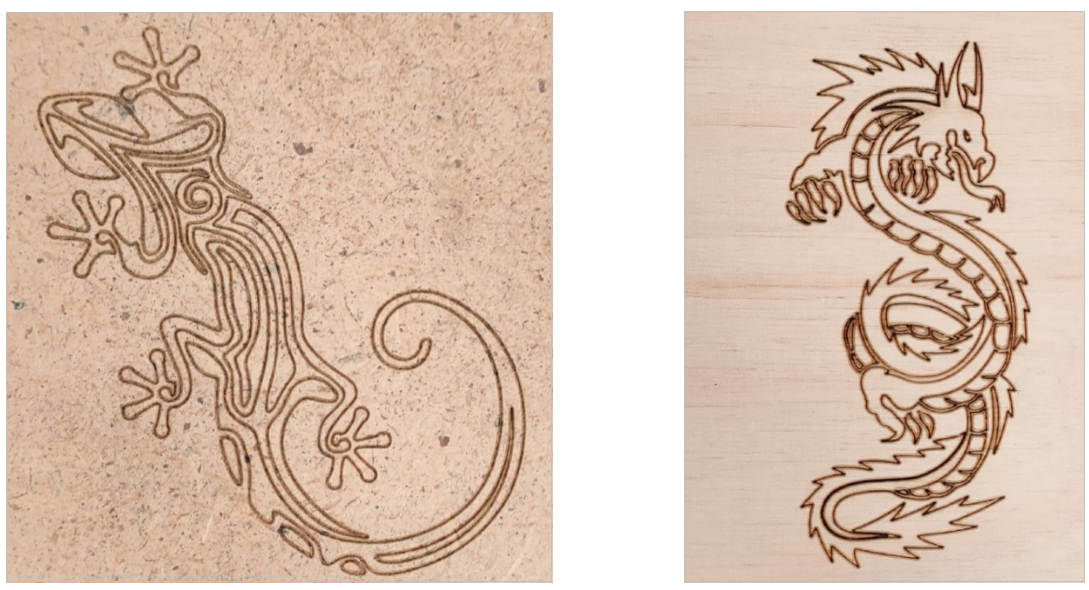
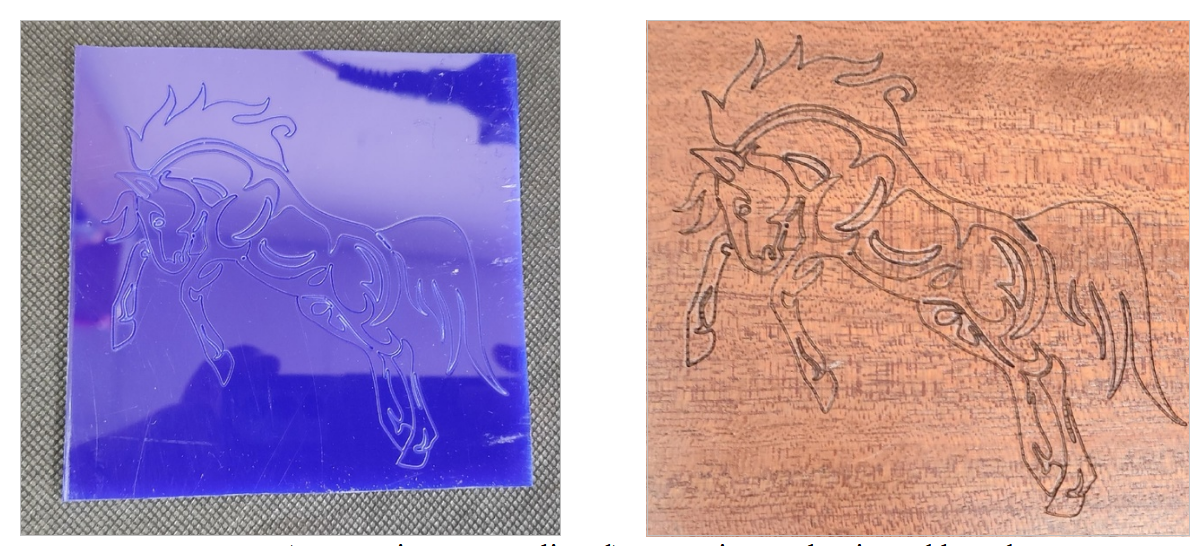
Figure 13 Outline Engraving Result
Conclusion: with this installation, you can engrave, but there are difficulties with cutting. Due to the deviation of the galvanometer beam, the cut is obtained at an angle, this may not be critical when cutting a single product, but when trying to cut a prefabricated product, this can cause problems when assembling the product. Fire may occur when cutting wood-based material.